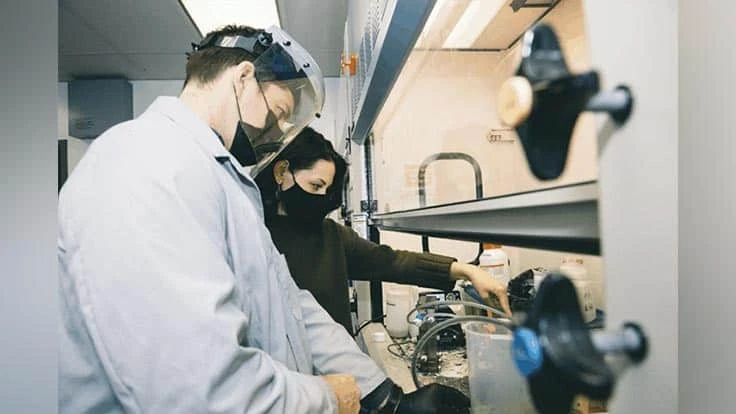
Photo courtesy of Nth Cycle
_fmt.png)
A number of companies have announced their intentions to recycle lithium-ion batteries (LIBs) in the United States. Many of these technologies involve hydrometallurgical processes that are in different phases of development, and their output could play a critical role in developing domestic supply chains to support North American battery manufacturing.
The battery problem
The U.S. has a LIB production problem. Despite the goals of President Biden’s administration to replace the federal government’s vehicle fleet with American-made electric vehicles (EVs) that use a minimum of 50 percent domestically produced components, China accounts for nearly 75 percent of global LIB manufacturing capacity, writes Gavin Thompson, Asia Pacific vice chair at U.K.-based Wood Mackenzie, in a report released Feb. 10. China’s share of the global LIB market also is set to increase in the short term as it builds out additional manufacturing capacity.
However, recent announcements by Ultium Cells LLC, a joint venture between Seoul-based LG Energy Solution and Detroit-based General Motors, will help to increase U.S. production of LIBs. Ultium has announced that it will build two LIB cell manufacturing plants in the United States: The first is under construction in Lordstown, Ohio, near a former GM assembly plant that is now home to electric fleet truck manufacturer Lordstown Motors Corp., and the second will be built in Spring Hill, Tennessee. These plants will manufacture LIBs for use in vehicles produced by GM, which announced earlier this year that it plans to offer 30 all-electric models globally by mid-decade, while 40 percent of its U.S. models will be battery electric by the end of 2025.
However, manufacturing investments such as these don’t address another problem associated with LIB production: The raw materials used in LIBs—lithium, nickel and cobalt—are produced largely outside of the U.S.
According to Wood Mackenzie’s base case scenario for mobility electrification, nickel production would need to increase by almost 70 percent by 2040, while cobalt and lithium production would need to grow by 200 percent and by 600 percent, respectively. China is better positioned than the U.S. when it comes to these natural resources, having increased its ownership of cobalt resources in the Democratic Republic of the Congo and lithium reserves in Chile and Indonesian nickel mines, Thompson writes, adding that China also has most of the global refining capacity for these metals.
With this in mind, battery manufacturers are investing to reduce the proportion of cobalt in batteries, he says, citing the work GM and LG are doing through Ultium to reduce use of the metal by 70 percent by increasing the amount of aluminum used. Panasonic and Tesla also are working to develop a cobalt-free battery, Thompson writes.
Additionally, Ultium has announced a partnership with Li-Cycle, a recycling company, that will help Ultium recover raw materials from its manufacturing scrap and that could unlock additional recycled material supply.
_fmt.png)
Li-Cycle’s hub-and-spoke model
Through Li-Cycle, Ultium Cells will be able to recycle scrap battery materials generated in the manufacturing process, including cobalt, nickel, lithium, graphite, copper, manganese and aluminum. Ninety-five percent of these materials can be used in the production of new batteries or in adjacent industries, according to a news release issued by GM in early May.
“Our combined efforts with Ultium Cells will be instrumental in redirecting battery manufacturing scrap from landfills and returning a substantial amount of valuable battery-grade materials back into the battery supply chain,” Ajay Kochhar, Li-Cycle president, CEO and co-founder, says in the news release. “This partnership is a critical step forward in advancing our proven lithium-ion resource recovery technology as a more sustainable alternative to mining.”
Kochhar tells Recycling Today the amount of scrap generated in LIB manufacturing can range from 5 percent to 10 percent. Ultium says its two sites each will have more than 30 gigawatt hours of annual capacity, with room to expand.
Mississauga, Ontario-based Li-Cycle was established in 2016 and is taking a hub-and-spoke approach to LIB recycling, with existing commercial spokes in Rochester, New York, and Kingston, Ontario. The company is developing its first commercial hub in Rochester, where it will use a hydrometallurgical process to recycle the black mass produced at its spokes.
Li-Cycle plans to construct 20 spoke facilities globally over the next five years and four hubs, Kochhar says, and the company recently announced the construction of its third spoke in Gilbert, Arizona, within the Phoenix Metro area. Once the Gilbert spoke is online, Li-Cycle will be able to process up to 10,000 metric tons of end-of-life batteries and battery manufacturing scrap annually at the site, bringing its total recycling capacity to 20,000 metric tons per year, the company says.
“We noticed that we need to be as nimble as we can to adapt to customers,” he says. “We have to be nimble and thoughtful about the buildout.”
Kochhar, who has a background in chemical engineering and formerly worked for Canada-based Hatch helping to develop lithium conversion projects, says Li-Cycle’s hub-and-spoke model solves the logistics problem associated with LIBs by decentralizing the mechanical processing of the batteries near generators, namely battery manufacturers and areas with high concentrations of EV use. The company also is working with aggregators of end-of-life electronics, he says. Its spokes produce black mass—a mixture of lithium, manganese, cobalt and nickel—as well as a mixed aluminum and copper product and plastics.
Under Li-Cycle’s business model, every hub would be fed by 12 spokes, Kochhar says. The spokes are “very deployable and easily permittable,” he adds. These sites shred the batteries using a process that involves “aqueous immersion,” according to one of the company’s patents, which helps to mitigate the thermal risk posed by the batteries.
Li-Cycle’s demonstration plant in Kingston processes the black mass using a “wet chemistry” process, Kochhar says, that enables the company to recover lithium carbonate, cobalt sulphate, nickel sulphate and manganese carbonate that can be used to manufacture new batteries or in other applications.
When selecting the locations for Li-Cycle’s hubs, he says access to a good labor pool with a knowledge of chemical processing and the ability to plug into existing infrastructure are key considerations. The company plans to break ground on its Rochester hub, which will be in the Eastman Business Park (also home to its Rochester spoke), in late 2021, with operations starting at the end of 2022 or in early 2023. When fully operational, the site will employ 120 people, Kochhar says.
As LIB production in North America increases, he says, Li-Cycle has the opportunity to work with these manufacturers on truly closed-loop recycling solutions, where a unit of lithium goes back to the same supply chain.

Nth Cycle’s closed-loop model
Boston-based Nth Cycle is exploring toll processing arrangements with mine operators and recyclers in North America using its electro-extraction technology to recover critical metals from end-of-life batteries and electronics, low-grade ore and mine tailings. The company recently secured $3.2 million in funding from investors led by Clean Energy Ventures, also based in Boston.
The company’s process uses electricity rather than hydro-metallurgy or pyrometallurgy to extract battery materials from black mass, Nth Cycle’s founder and CEO Megan O’Connor says.
The system “is based on an electrochemically modified filter press, combining both filtration and electrowinning into one unit,” Nth Cycle’s website states. “This allows for operation at low voltages and high current efficiencies, significantly reducing energy costs and footprint. In addition, the in situ base production alleviates the need for highly caustic chemicals while reducing waste, potential hazards and greenhouse gas emissions.”
Nth Cycle’s technology was developed in 2017 by doctorate students at Harvard and Yale universities. O’Connor says she was a scribe during the Green Electronics Summit at Yale, which included presentations from companies such as Apple and Dell. “Recycling kept coming up over and over again,” she says. O’Connor says she changed her doctoral project to help address the issue and has been working to commercialize the technology.
The company will use the funding it has received to deploy several pilot projects with recyclers and mine operators early next year. Nth Cycle says battery recyclers, operators of existing and proposed mines, automotive original equipment manufacturers, micromobility companies and battery manufacturers are interested in the technology to reduce their reliance on imported critical metals or environmentally unfriendly recovery technologies.
O’Connor says that if the Biden administration can realize its goals for vehicle electrification and green energy, alternative sources of critical metals will be needed because of global supply chain issues. Her company’s technology can recover these metals from end-of-life products as well as help North American mines, which yield lower grades of some of these critical metals, to upgrade material in a cost-competitive way, “enabling a new supply chain,” she says.
Nth Cycle’s technology is modular with a minimal footprint, O’Connor says, though it can accommodate high volumes of feedstock. A typical unit requires 300 square feet and can process 500 tons annually.
She says Nth Cycle’s technology produces minimal waste. “All byproducts can be sold as secondary products. Our mission was to create technology that didn’t create more waste.”
Nth Cycle says its technology “can be tuned to capture a wide variety of transition, rare earth and precious metals.” Its metal hydroxides can be sold to hydrometallurgical refineries for reuse in lithium-ion cathode manufacturing, saving time, cost and resources in the production of battery-grade precursors.
O’Connor says Li-Cycle and Redwood Materials, the company co-founded by former Tesla executive JB Straubel, “are very focused on the logistics play,” capturing batteries from generators to produce black mass that they then refine.
Nth Cycle’s business model, however, is focused on on-site toll processing arrangements with companies that are producing black mass or mines. She views this approach as “more economical and sustainable,” eliminating the need for transportation. “Transportation is expensive and hazardous,” O’Connor says. “We can go where the batteries are.”
Dan Goldman, a co-founder and managing director of Clean Energy Ventures, says the company invested in Nth Cycle because its process is “so much more efficient than any battery recycling technology on the market” and “elegant in its simplicity.” He adds that Nth Cycle’s process is easily scalable with the ability to process everything from black mass to mining ores and tailings.
Also “particularly compelling” about Nth Cycle, Goldman says, is the company’s ability to reduce vulnerability around global supply chains. “We have to have production in this country. It creates jobs and economic opportunity and solidifies the supply chain so we can make things here and are not dependent on China and other parts of the world,” he says. Goldman adds that manufacturers such as GM, Ford and Apple also have a bias toward avoiding sourcing from unstable countries that also might use child labor.
_fmt.png)
A networked approach
Aqua Metals, a McCarran, Nevada-based company that has developed technology to recycle lead-acid batteries, says it has invested $2 million, paid in Aqua Metals stock shares, for a 10 percent ownership stake in LiNiCo Corp., a Nevada-based company focused on closed-loop LIB recycling.
LiNiCo has the U.S. exclusive license to use technology from Green Li-ion Pte Ltd., based in Singapore. LiNiCo also has a 20 percent ownership stake in Green Li-ion, with representation on its board.
Green Li-ion says its technology can “recycle a myriad of LIB types at once using one machine alone, the GLMC-1.”
The GLMC-1 technology is based on a co-precipitation sequence that allows the recovery of cathode metal salts, without separation of the metal elements, “speeding up the recycling process by two to three times,” according to Green Li-ion. These metal salts are the precursor for synthesis of new cathode material that can form the basis for new LIBs.
The technology can be used to enhance existing LIB recycling processes or can be used as a stand-alone system for recycling and cathode manufacturing, according to the company.
LiNiCo says it plans to increase its ownership stake in Green Li-ion and further develop its own sustainable clean technologies. It plans to produce 10,000 metric tons of pure cathode in the next three years.
Aqua Metals says its investment in LiNiCo is part of its strategy to grow by potentially applying its AquaRefining process to LIB recycling.
LiNiCo is leasing, with additional purchase deposits to buy, part of Aqua Metals’ 136,000-square-foot facility in McCarran. “This noncore asset disposition was driven by the company’s accelerated focus on its equipment supply and licensing strategy,” Aqua Metals says of the lease agreement.
Steve Cotton, CEO of Aqua Metals, says Green Li-ion’s hydrometallurgical technology is “complementary” to Aqua Metals’ technology. Additionally, Aqua Metals filed a provisional patent for recovering high-value metals from recycled LIBs using AquaRefining, saying early- phase testing shows its methodology that originally was developed to plate lead from lead-acid batteries can be used to plate the high-value metals found in LIBs, such as cobalt, nickel and manganese.
Cotton says LIBs present a challenge “that no one company can solve alone,” which is why it has formed an “eco network” with LiNiCo, Green Li-ion and Comstock Mining.
Michael Vogel, president, CEO and founder of LiNiCo, agrees. “It’s important that we form these coalitions because they are stronger than being a one-man band.”
He says Green Li-ion’s technology “produces a higher grade product that skips the steps involved in the extraction of individual battery metals, such as pure lithium, nickel and cobalt, to produce pure cathode,” which takes steps out of the battery manufacturing process. Using its own process, LiNiCo also can recover the individual battery metal salts, giving the company five possible revenue streams.
LiNiCo’s process involves four other stages before the material enters the Green Li-ion system, Vogel says. They include shredding the LIBs; drying and gas cleaning; a separation process that removes secondary materials, such as copper, aluminum, steel and plastics, to isolate the black mass, which then goes through additional processing and purification before being fed to the Green Li-ion system.
He says the company’s goal is to produce 2 tons per day of 99 percent pure cathode per machine, with 20 machines on order. Within three years, LiNiCo plans to produce 10,000 tons annually. “Every 1,000 tons of batteries will produce approximately half a ton of cathode material,” Vogel says. “We are going to need 20,000 tons of batteries to produce 10,000 tons of cathode in a single year.”
LiNiCo intends to expand its facilities in the U.S., Vogel says, and potentially could license additional technologies, such as AquaRefining.
Comstock Mining Inc., based in Virginia City, Nevada, has a 45 percent ownership stake in LiNiCo presently, he says.
Corrado DeGasperis, who is Comstock’s chairman of the board, director and chief executive officer, says the company’s stake in LiNiCo is part of its “transformational green shift,” which also includes its global mercury remediation and other renewable natural resource projects.
While Comstock says it has historically focused on the extraction of precious and strategic metals, it now believes “the global clean energy transition, escalating population growth and accelerating natural resource scarcity is converging into a ‘perfect storm’ of global demand for a broader array of strategic materials.” Therefore, Comstock’s strategic focus is expanding to include “the extraction and valorization of a portfolio of critical and inevitably scarce materials, with an initial preference for high cash throughput generators that complement our existing competencies and operations.”
Regarding the eco network Comstock has formed with LiNiCo, Aqua Metals and Green Li-ion, DeGasperis says, “It feels like we are one company with a common goal. It feels like we have something more cohesive, more competent. It feels better to have all of these resources together.”
While he says Aqua Metals and LiNiCo are “well ahead in the race” to commercialize LIBs recycling, DeGasperis adds, “I’m not sure there are going to be winners and losers in the LIB space” because of the volume of material that will be available. “I hope everyone is successful—I hope LiNiCo is the most successful.”
The headquarters of LG Energy Solution initially were misidentified as being in Taiwan.
Get curated news on YOUR industry.
Enter your email to receive our newsletters.
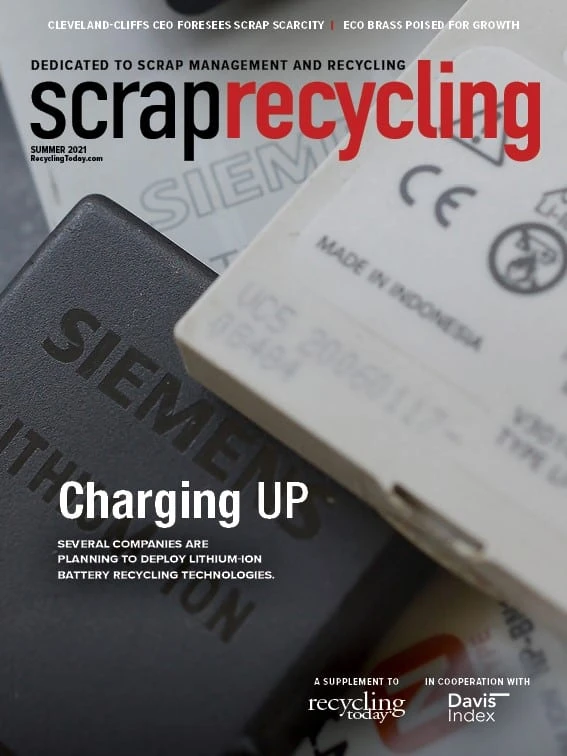
Explore the Summer 2021 Scrap Recycling Issue
Check out more from this issue and find your next story to read.
Latest from Recycling Today
- Nucor expects slimmer profits in early 2025
- CP Group announces new senior vice president
- APR publishes Design Guide in French
- AmSty recorded first sales of PolyRenew Styrene in 2024
- PRE says EU’s plastic recycling industry at a breaking point
- Call2Recycle Canada, Staples Professional expand partnership
- Circular Services breaks ground on north Texas MRF
- Tariff uncertainty results in choppy nonferrous scrap flows